Otimizando o tamanho do portão e localização em um molde de injeção de bomba de loção através da análise do fluxo do molde envolve um processo sistemático de simulação, análise e ajustes de projeto. Aqui está um guia passo a passo para alcançar essa otimização:
1. Defina as metas e critérios do projeto:
- Comece definindo claramente os objetivos e critérios do molde de injeção da bomba de loção. Considere fatores como qualidade da peça, tempo de ciclo, uso de material e restrições de custo.
2. Colete dados de materiais:
- Obtenha dados precisos do material para a resina plástica específica a ser usada no processo de moldagem por injeção. Isso inclui índice de fluidez (MFI), viscosidade, propriedades térmicas e outras características do material.
3. Criação de modelo:
- Crie um modelo 3D detalhado da peça da bomba de loção e do molde de injeção, incluindo a cavidade, núcleo, canais de resfriamento e sistema de corredor. Certifique-se de que o modelo represente com precisão as condições de produção pretendidas.
4. Configuração da simulação:
- Utilize software de análise de fluxo de molde para configurar a simulação. Defina os parâmetros do processo de moldagem por injeção, como pressão de injeção, perfis de temperatura e taxas de resfriamento. Especifique os locais dos portões e os tamanhos iniciais dos portões.
5. Execução inicial da simulação:
- Execute a simulação inicial do fluxo do molde com os locais e tamanhos de comporta escolhidos. Analise os resultados, incluindo tempo de enchimento, distribuição de pressão, linhas de solda e locais de retenção de ar. Identifique quaisquer possíveis problemas ou áreas de melhoria.
6. Análise de localização do portão:
- Avaliar a adequação dos locais de portão escolhidos. Considere fatores como preenchimento equilibrado de cavidades, prevenção de defeitos cosméticos e minimização do impacto das linhas de solda. Ajuste os locais dos portões conforme necessário.
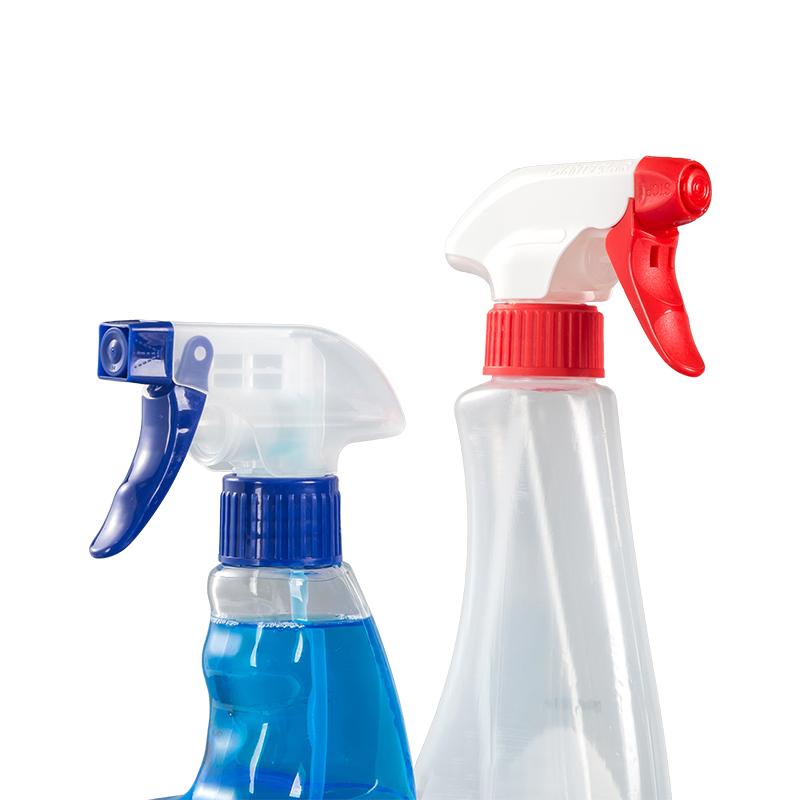
7. Análise do tamanho do portão:
- Analisar o efeito do tamanho da porta no processo de injeção. Aumente ou diminua gradualmente os tamanhos das comportas em simulações subsequentes para encontrar o tamanho ideal que equilibre o tempo de enchimento, a pressão e o fluxo de material sem causar defeitos.
8. Seleção do tipo de portão:
- Dependendo dos resultados da análise do tamanho da comporta, escolha o tipo de comporta apropriado, como comporta de canal de entrada, comporta de borda ou comporta em leque. O tipo de porta afeta a forma como o material entra na cavidade e pode afetar a qualidade da peça.
9. Otimização do sistema Runner:
- Otimize o projeto do sistema de canais para garantir uma distribuição uniforme do material em todas as cavidades. Ajuste as dimensões e configurações do corredor para minimizar o desperdício de material e a queda de pressão.
10. Análise do Canal de Resfriamento:
- Avalie o impacto da localização e tamanho do portão na eficiência do resfriamento. Certifique-se de que a configuração da porta escolhida não interfira na eficácia dos canais de resfriamento. Ajuste o posicionamento do canal de resfriamento, se necessário.
11. Simulação Iterativa:
- Realize simulações iterativas, fazendo ajustes graduais nas localizações e tamanhos dos portões com base nos resultados da análise. Continue a refinar o projeto até que os critérios desejados, como enchimento equilibrado e defeitos mínimos, sejam atendidos.
12. Validação Final:
- Realize uma análise final do fluxo do molde para validar o tamanho e a localização otimizados da porta. Confirme se o design atende aos objetivos e critérios predefinidos do projeto.
13. Documentação e Relatórios:
- Documente os resultados, incluindo a configuração do portão escolhida, dados de simulação e quaisquer ajustes de projeto. Prepare um relatório resumindo o processo de otimização e seus resultados.